
Cooperative Navigation
Intelligent cooperative navigation for industrial autonomous guided vehicles (AGVs)
Applicationcenter Fraunhofer IPA Stuttgart
This use case shows the capabilities of Virtual Fort Knox in the context of Cloud Robotics. We demonstrate the Intelligent cooperative navigation for industrial autonomous guided vehicles (AGVs). This improves the overall efficiency of industrial transport systems by optimal routing of all involved vehicles. Also the costs of the system can be reduces becaus the required sensors no longer need to be carried by the vehicles but can only be added to places that require precise localization. The Manufacturing Service Bus allows effective communication between the vehicle, the cloud server, external sensors and the manufacturing system.
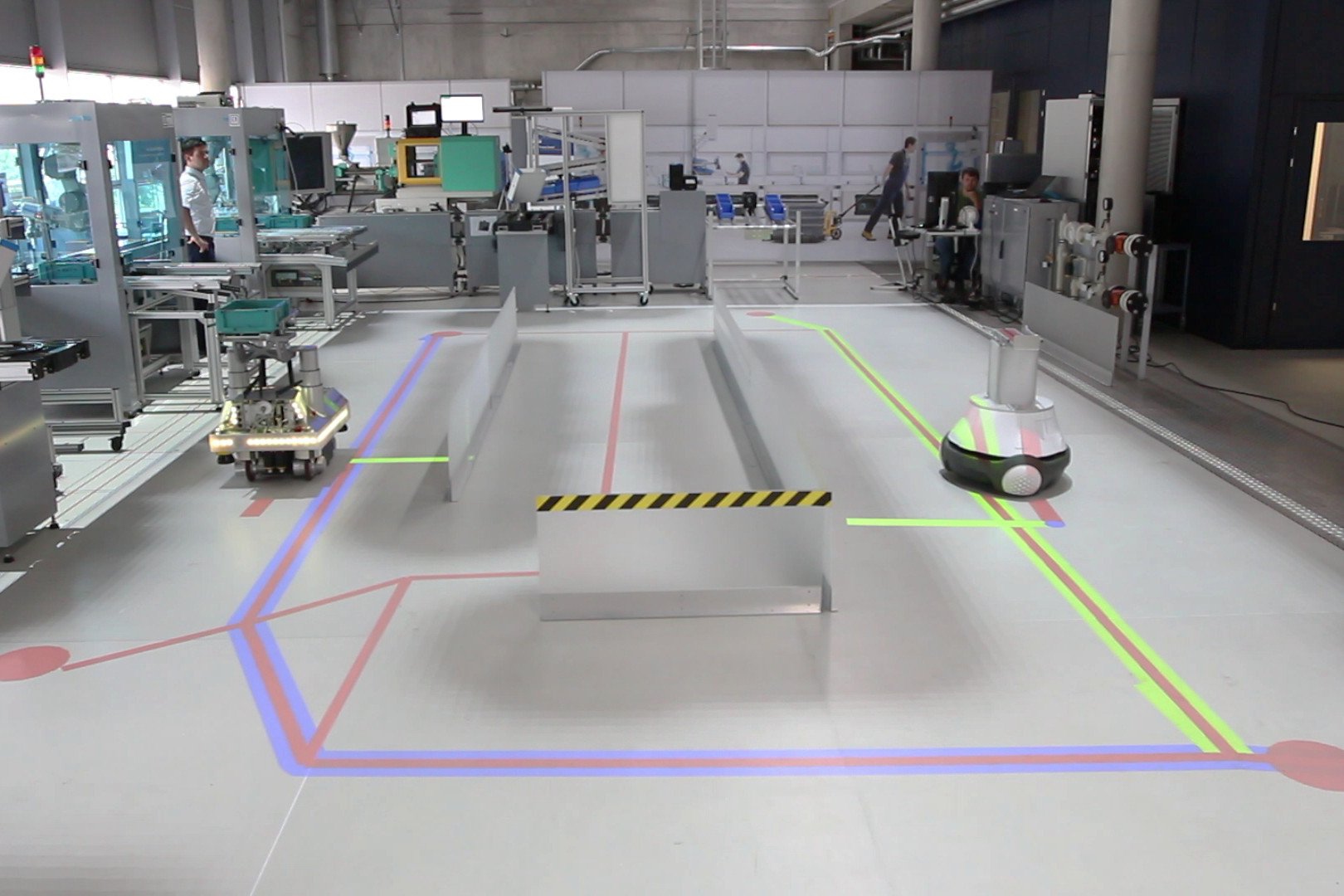
The architecture of the system is designed to allow for both the shifting of computation to the cloud but also to cooperative plan for all vehicles on the Holistic Environment Model that incorporates all environmental data. The navigation receives one goal per vehicle to plan a route to. These routes are calculated for the full fleet of vehicles in a fashion that the vehicle take each others position into account at any point in time. It produces a set of paths, one for each vehicle.
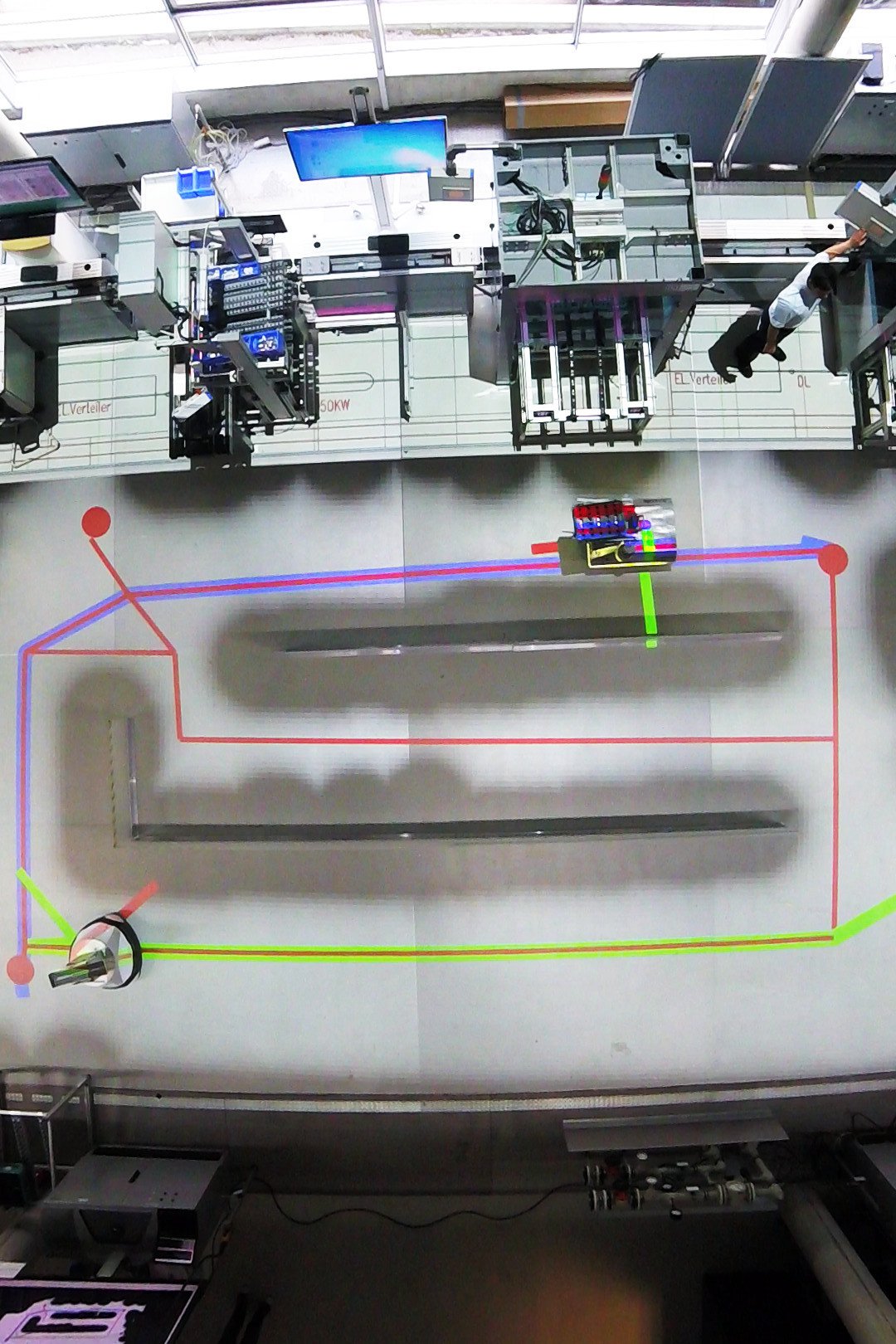
The planning is done using all data available from any vehicle and all external sensors. This makes vehicles avoid obstacles even if itself can not sense the obstacle itself. These sensors must not be installed manually for the system. Lidar Sensors are also commonly used at safety sensors and exist in production environments already. Utilizing the MSB, these can be integrated into the system.
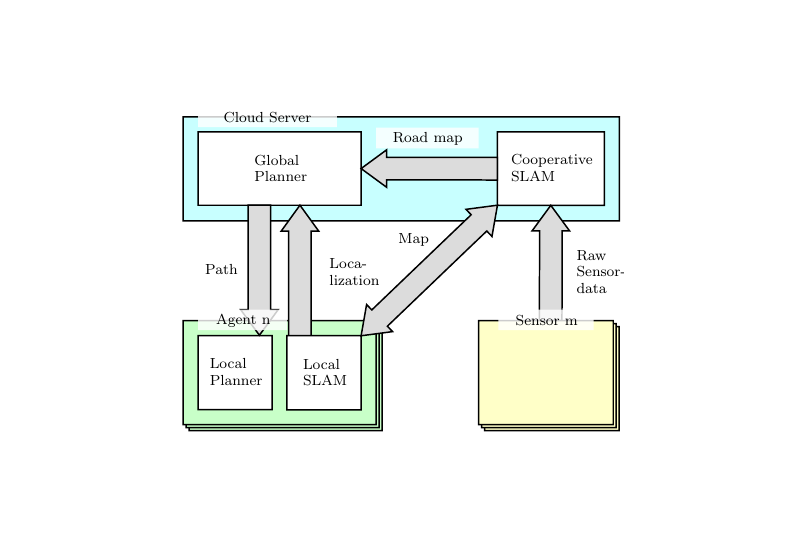
The Manufacturing Service Bus allows the communication between the vehicles and their cloud server. Additionally it is used to receive data form the external sensors or to interface the manufacturing infrastructure. For example this communication can be necessary when passing transport goods to a manufacturing station as visible in the video. The usability of the MSB allows for flexibility by easy reconfiguration of the system.
Read more about "Industrial and commercial service robots" on the Fraunhofer Institute for Manufacturing Engineering and Automation IPA homepage.